Um das richtige Siebgewebe zu wählen, muss man verstehen, wie es sich abnutzt. Im Gebrauch neigen die Siebe durch den Abrieb der Materialien dazu, flacher zu werden, indem sie die Reliefs erodieren. Die Abriebfestigkeit zur Bekämpfung des Verschleißes von Siebmedien ist daher ein wichtiges Ziel bei der Auswahl von Siebmedien. Dabei spielen mehrere Variablen eine Rolle:
- Die Art der Materialien, die für die Herstellung der Siebe verwendet werden : metallisch vs synthetisch
- Das Aussehen der Oberfläche, die mit dem zu siebenden Produkt in Berührung kommt
- Die Qualität der Werkzeuge und der Herstellungsprozess von Siebgeweben
Die Wahl des Stahls
Eine ISO-Norm legt die Voraussetzungen für die Herstellung von Siebgeweben fest (Toleranzen, Anforderungen, Prüfverfahren usw.). Die europäische Bezeichnung für ein Gewebe aus hochfestem Stahldraht kann verwirrend sein, da sie für Drähte mit einer Festigkeit von mehr als 80 kg/mm² verwendet wird. Diese Bezeichnung allein reicht nicht aus, um Siebgewebe von verschiedenen Herstellern vergleichbar zu machen.
Gewebte Siebgewebe werden heute überwiegend aus einer einzigen Stahldrahtsorte hergestellt, die umgangssprachlich als "Siebdraht" bezeichnet wird. Tatsächlich handelt es sich dabei um einen Kohlenstoffstahl, der den Federstahldrähten sehr ähnlich ist und dessen Endfestigkeit durch Kaltziehen erreicht wird.
Für die Herstellung seiner Siebgewebe, GIRON hat Stähle mit optimierten Eigenschaften ausgewählt mit einem Kohlenstoffgehalt von mindestens 0,5%, um eine hohe Verschleißfestigkeit zu gewährleisten, und einer hohen Elastizität, die ein Absorbieren ohne Brüchigkeit ermöglicht:
- Die Verformungen, die für die Vorformung der Garne vor dem Weben notwendig sind
- Mechanische Belastungen, die durch Vibrationen der Siebe verursacht werden, auch bei hoher Energie
- Stöße von Materialien und Produkten, die auf den Gittern zirkulieren
Das Oberflächenbild aus der Vorformung
Wie bereits erwähnt, entsteht der abrasive Verschleiß durch die Reibung des Materials auf der Siebfläche. Es ist daher leicht nachvollziehbar, dass je flacher die Oberfläche ist, desto weniger trifft das Siebgut auf Erhebungen, an denen es knabbern kann.
Die Art der Vorformung hat daher eine starke Bedeutung für die Verringerung des Verschleißes der Siebgewebe, deren Lebensdauer von der Materialmenge abhängt, die verschlissen werden kann, ohne dass sich die Maschen verformen und die Drähte sich lockern.
1. Die Vorform "einfache Welle" (Modell : Grilgirco)
Diese Vorform entspricht den Formen A, B und C, die in der Norm ISO4783/3 definiert sind. Sie stellt die grundlegendste Form der Wellung eines Drahtes dar. Dabei wird der Stahldraht in eine einfache Sinusform verformt.
Das Weben dieser Fäden (Ketten und Schüsse) bewirkt, dass eine Oberfläche entsteht, die aus Erhebungen und Vertiefungen für einen Höhenunterschied besteht, der einem Fadendurchmesser entspricht.
Aufgrund des relativ offenen Schließwinkels im Bereich der Wellen ist diese Art der Vorformung offensichtlich umso stoßempfindlicher, je größer das Verhältnis von Maschen zu Garn ist.
Außerdem behindert unter dem Einfluss von Abrieb die Erosion oder Abnutzung der Wellenköpfe (Beulen) den Produktvorschub und führt zum Fadenbruch, bevor die Siebfläche wirklich abgenutzt ist.
Aus Gründen der Herstellungskosten wird diese Vorform jedoch häufig für die kleinsten Maschenöffnungen und die feinsten Schnitte verwendet, d. h. in der Regel weniger als 10 mm.
2. Die Vorform "Halbschlitzwelle" (Modell : Plangirco)
Diese Vorformung entspricht der Form D, die in der Norm ISO4783/3 definiert ist. Diese gerade Welle stellt eine Weiterentwicklung der einfachen Welle (Form A) dar.
Die Suche nach einer besseren Abriebfestigkeit führte zur Entwicklung einer Vorformtechnik, die sich durch einen stärkeren Abdruck an den Kreuzungspunkten der einzelnen Fäden auszeichnet.
Das Weben dieser Drähte (Ketten und Schüsse) bewirkt, dass Erhebungen (Beulen) begrenzt werden, indem so viel Metall wie möglich auf die Arbeitsfläche übertragen wird, wobei der Höhenunterschied auf ½ Drahtdurchmesser begrenzt ist.
Dadurch wird die Lebensdauer des Tuches im Vergleich zu einer einfachen Wellung verbessert. Diese Art der Vorformung "halbe Kerbe" wird üblicherweise über Maschenöffnungen von 10 mm hinaus verwendet.
3.Die Vorform "Wellenförmige flache Oberfläche" (Modell : Plangirco flache Oberfläche)
Diese Vorformung entspricht der Form E, die in der Norm ISO4783/3 definiert ist. Diese Wellung ist die letzte Perfektionierung der Vorformung des Garns auf der Suche nach maximale Lebensdauer der Siebe. Die Siebfläche hat nicht nur kaum noch Erhebungen (Beulen), sondern es wird auch das meiste verfügbare Metall auf die Arbeitsfläche übertragen.
Durch eine Kombination aus einer Stanzung mit geschlossenem Winkel und einem Gesenkschmieden der Drähte an jedem Kreuzungspunkt beseitigt diese Vorformung jedes Risiko einer Verformung der Siebfläche bis zur vollständigen Abnutzung des Gitters.
Diese Vorformung "ebene Oberfläche" ist natürlich wirksam in ihrem bevorzugten Bereich der mittleren Schnitte und Maschen (10 bis 40 mm), wo die von den Normen der Zuschlagstoffe geforderte Schnittgenauigkeit und die Verschleißfestigkeit durch Abrieb ausschlaggebend sind.
Die in zahlreichen Installationen kontrollierte Lebensdauer garantiert eine unübertroffene Haltbarkeit und mindestens 30% bis 50% mehr als jede andere Art von Preforming.
GIRON verwendet diese Vorform "flache Oberfläche" als Standard ab einer Maschenweite von 8 mm und für alle Maschen, in denen Garne mit einem Durchmesser zwischen 4 mm und 8 mm verwendet werden.
Die Qualität der Werkzeuge und der Herstellungsprozess von Siebgeweben
Die Qualität des Stahldrahts und die Art der Vorformung sind zwar sehr wichtig, reichen aber bei weitem nicht aus, um ein sehr gutes Siebgewebe zu erhalten. Wenn die Werkzeuge nicht gut konstruiert sind und die Maschinen nicht die erforderliche Leistung und Präzision aufweisen, werden die Maschen nicht gleichmäßig sein, und die Drähte werden sich bei der Arbeit lockern und durch Einlaufen vorzeitig verschleißen.
Auch die Gesellschaft GIRON hat seine eigenen einzigartigen Maschinen, Verfahren und Techniken entwickelt und perfektioniert. die die Herstellung von hochwertigen Stahlgittern ermöglicht.
Die Wahl des Materials
Es gibt heute keine spezifische Norm, die die Voraussetzungen für die Herstellung von Siebgeweben aus synthetischen Materialien festlegt (Toleranzen, Anforderungen, Überprüfungsmethoden...). In diesem Bereich werden zwei Grundstoffe verwendet: Gummi und Polyurethan.
Aber wie definiert man ein gutes Ausgangsmaterial für die Herstellung von Sieben.
1. Der Kautschuk
Kautschuk ist das Ergebnis der Verarbeitung und homogenen Mischung mehrerer Zutaten unterschiedlicher Herkunft und Beschaffenheit. Ursprünglich wurde Kautschuk aus Naturlatex hergestellt, der von bestimmten Pflanzen (Gummibaum) stammt. Mit der industriellen Entwicklung und neuen Techniken kann Kautschuk auch synthetisch hergestellt werden (SBR, NBR usw.), die aus Derivaten fossiler Stoffe gewonnen werden.
Durch komplexe Formulierungen und Mischungen können heute je nach Anwendung technische und leistungsfähige Kautschuke hergestellt werden.
Die wichtigsten Eigenschaften von Gummi sind seine Elastizität, seine Dichtigkeit und seine Dämpfung. Diese drei Parameter sind im Bereich der Siebung interessant, vor allem bei der Verarbeitung von groben Körnungen, um Stöße zu absorbieren oder auch den Lärm zu verringern.
Es gibt noch weitere Parameter, die berücksichtigt werden müssen, wie z. B. die Reißfestigkeit, die Hitzebeständigkeit, die chemische Beständigkeit, die Verarbeitung während des Vulkanisierungsprozesses und die Bedingungen für die Siebung.
Gummi hat also gute Eigenschaften für die Beständigkeit gegen Verschleiß durch Verformung und/oder Schnitt. Allerdings muss die Dicke ausreichend sein, um den Aufprall des Materials auf die Siebfläche zu absorbieren. Darüber hinaus spielt auch der Aufprallwinkel des Materials eine entscheidende Rolle für den Verschleißgrad, insbesondere für die Reißfestigkeit.
GIRON arbeitet ständig mit seinen Lieferanten zusammen, um die optimale Formulierung seiner Produkte zu definieren. Hochleistungskautschuke je nach Anwendung wie das Sieben von heißen Produkten, Chemikalien, abrasiven Produkten.
2. Das Polyurethan
Polyurethane (eine Familie von Polymeren) wurden in den 1930er Jahren in Deutschland entwickelt und nach dem Zweiten Weltkrieg als Ersatz für Nylon oder Gummi weit verbreitet.
Polyurethan (Urethanfunktion) ist das Ergebnis der chemischen Reaktion eines Isocyanats und eines Polyols.
Es gibt drei große technische Familien: Weichschaumstoffe, Hartschaumstoffe und Nicht-Schaumstoffe.
Schaumstoffe machen 2/3 des Marktes aus.
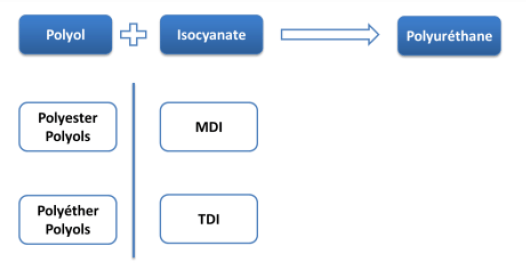
Ende der 1970er Jahre hielt Polyurethan (Familie der Nicht-Schaumstoffe: Elastomere, Klebstoffe, Beschichtungen) Einzug in die Sieb- und Materialbearbeitungstechnologie.
Wie Gummi wird auch Polyurethan aus komplexen chemischen Mischungen und Formeln hergestellt, bei denen durch die Wahl der Inhaltsstoffe je nach Anwendung unterschiedliche Leistungsniveaus erreicht werden können. Alles ist eine Frage des Kompromisses.
Je nach Siebbedingungen und Art des Materials können wir also die Eigenschaften der Polyurethan-Gitter.
Der Abriebverlust nach DIN 53516 ermöglicht theoretisch einen Vergleich der Leistung verschiedener Polyurethansorten. Die Auswahl der besten Sorte beruht daher meist auf der Erfahrung des Herstellers oder auf der internen Entwicklung von Testverfahren, die der Realität am nächsten kommen.
Unabhängig von der Wahl der Sorte hat die Wahl der Härte (ausgedrückt in Shore) eine große Bedeutung für die Abriebfestigkeit. Die Art, Form und Masse des gesiebten Materials führt zu mehr oder weniger scharfen Schlägen, die von geringeren Härtegraden grundsätzlich besser verkraftet werden. Daher werden häufig Zweischichtkonstruktionen verwendet.
In unserem Fall sind die verwendeten Polyurethane heiß gießbar und aufgrund der Anforderungen sowohl an die Mischungsverhältnisse der einzelnen Komponenten als auch an die Verarbeitungstemperaturen ist der Einsatz von Gießmaschinen fast immer unerlässlich.
Die Abriebfestigkeit der Siebfläche hängt direkt davon ab, ob die vom Materiallieferanten empfohlenen Verarbeitungsbedingungen eingehalten werden (z. B. Formtemperaturen, Brenntemperatur und -zeit, Dämpftemperatur und -zeit). Auch hier wird die Erfahrung und Sorgfalt während des Prozesses die Endqualitäten des Produkts garantieren.
GIRON bemüht sich daher ständig um die Entwicklung und Herstellung von Materialien, die in Bezug auf die Abriebfestigkeit immer besser werden. Wir arbeiten regelmäßig mit unseren Lieferanten zusammen, um die optimale Formulierung unserer Produkte zu definieren. Hochleistungspolyurethane je nach Anwendung, z. B. Absieben von abrasivem Material, Absieben unter Wasser oder im Trockenen, oder viele andere.