To choose the right screen cloth, you need to understand how it wears. In use, the abrasion of materials tends to flatten screens, eroding the relief. Abrasion resistance to combat the wear and tear of screening media is therefore a key objective in this choice. Several variables come into play:
- The type of materials used to manufacture the sieves: metal vs. synthetics
- The appearance of the surface in contact with the product to be screened
- The quality of tooling and the screen cloth manufacturing process
The choice of steel
An ISO standard defines the prerequisites for the manufacture of screening cloths (tolerances, requirements, verification methods, etc.). The European designation of high-strength steel wire cloth can be confusing, since it is accepted for wires with a strength of over 80 kg/mm². This designation alone is not sufficient to make screening cloths from different manufacturers comparable.
Today, most woven screen cloths are made from the same grade of steel wire, commonly referred to as "screen wire". This is carbon steel, very similar to spring steel wire, whose final strength is obtained during the cold-drawing process.
For the manufacture of its screening cloths, GIRON has selected steels with optimized characteristics combining a carbon content of at least 0.5% to guarantee high wear resistance, and high resilience to absorb without brittleness:
- The deformations required to preform wires before weaving
- Mechanical stresses caused by screen vibrations, even at high energies
- Impacts from materials and products passing over the grilles
The surface appearance resulting from preforming
As mentioned above, abrasive wear occurs when materials rub against the screening surface. It is therefore easy to understand that the flatter the surface, the less relief the product to be screened will encounter.
The type of pre-forming is therefore of great importance in reducing wear on screening cloths, whose service life depends on the amount of material that can be worn away without the meshes becoming deformed or the wires loosening.
1. The "simple wave" preform (model : Grilgirco)
This preform corresponds to the A, B and C shapes defined by ISO4783/3. It represents the most elementary form of wire corrugation. The operation consists in deforming the steel wire into a simple sinusoidal shape.
The weaving of these threads (warps and wefts) produces a surface composed of bumps and hollows for a difference in level equal to one thread diameter.
Because of the relatively open angle of closure at the corrugations, this type of preform is obviously all the more sensitive to shocks the higher the mesh-to-wire ratio.
What's more, under the effect of abrasion, erosion or wear of the corrugation heads (bumps) impedes product advancement and leads to wire breakage before the screening surface is actually worn.
For manufacturing cost reasons, however, this preforming process is commonly used for the smallest mesh openings and finest cuts, generally less than 10 mm.
2. The "half-notch wave" preform (model : Plangirco)
This preform corresponds to the D shape defined by ISO4783/3. This straight corrugation is an evolution of the simple corrugation (form A).
The search for improved abrasion resistance led to the development of a preforming technique characterized by a more pronounced imprint at the crossing points of each wire.
The weaving of these wires (warps and wefts) has the effect of limiting relief (bumps) by transferring as much metal as possible towards the work surface, with a difference in level limited to ½ wire diameter.
As a result, the fabric will last longer than with a single corrugation. This type of "half-notch" preforming is commonly used beyond 10 mm mesh openings.
3.flat surface corrugation preforming (model : Plangirco flat surface)
This pre-shaping corresponds to the E-shape defined by ISO4783/3. This corrugation is the ultimate wire preforming refinement in the quest for maximum screen life. Not only is the screening surface virtually free of bumps, but the maximum amount of available metal is transferred to the working face.
The combination of closed-angle stamping and wire stamping at each crossing point eliminates any risk of deformation of the screening surface until the grid is completely worn.
This "flat surface" preforming is naturally effective in its preferred field of medium-mesh cuttings (10 to 40 mm), where the precision of cut required by aggregate standards and resistance to abrasive wear are decisive.
Controlled service life on numerous installations guarantees unrivalled longevity, at least 30% to 50% longer than any other type of preform.
GIRON uses this "flat surface" pre-forming as standard from 8 mm mesh and for all meshes using wire diameters between 4 mm and 8 mm.
The quality of tooling and the screen cloth manufacturing process
The quality of the steel wire and the type of pre-forming, although very important parameters, are far from sufficient to obtain a very good screening mesh. If the tooling is not well designed, if the machines are not powerful enough and precise enough, the mesh will not be regular, and the wires will loosen during operation and wear prematurely due to running-in.
The company GIRON has developed and perfected its own unique machines, processes and techniques. for the manufacture of top-quality steel grids.
Choice of material
At present, there are no specific standards defining the requirements for the manufacture of screening cloths in synthetic materials (tolerances, requirements, testing methods, etc.). Two basic materials are used in this field: rubber and polyurethane.
But how do you define a good base material for sieves?
1. Rubber
Rubber is the result of the transformation and homogeneous blending of several ingredients of different origin and nature. Originally, rubber was made from the natural latex of certain plants (rubber trees). With industrial evolution and new techniques, rubber can also be made synthetically (SBR, NBR, etc.) from derivatives of fossil materials.
Today's complex formulation and blending processes make it possible to produce technical, high-performance rubbers for a wide range of applications.
The main properties of rubber are elasticity, tightness and damping. These three parameters are of particular interest in the field of screening, especially when processing large granulometries to absorb shocks or reduce noise.
However, the need to combat wear remains paramount, and other parameters also need to be taken into consideration, such as resistance to tearing, heat and chemical agents, its use in vulcanization processes and screening conditions.
Rubber therefore has good properties for resistance to wear caused by deformation and/or cutting. However, the thickness must be sufficient to absorb the impact of the material on the screening surface. In addition, the angle of impact of the material also plays a key role in the level of wear, particularly its resistance to tearing.
GIRON also works constantly with its suppliers to define the optimum formulation for its products. high-performance rubbers depending on the application, e.g. screening hot products, chemicals, abrasive products.
2. Polyurethane
First introduced in Germany in the 1930s, the use of polyurethanes (a family of polymers) became widespread after the Second World War, replacing nylon or rubber.
Polyurethane (urethane function) is the result of the chemical reaction of an isocyanate and a polyol.
There are three main technical families: flexible foams, rigid foams and non-foams.
Foams account for 2/3 of the market.
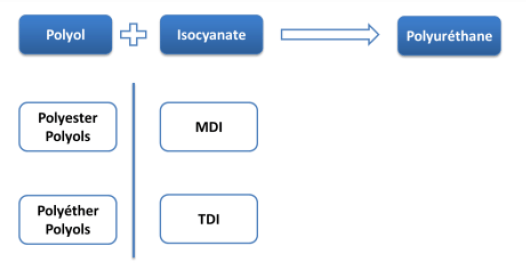
It was in the late 1970s that polyurethane (a family of non-foams including elastomers, adhesives and coatings) made its appearance in materials screening and processing technology.
Like rubber, polyurethane is the product of complex chemical mixtures and formulas, where the choice of ingredients enables different levels of performance to be achieved depending on the application. It's all a question of compromise.
Depending on the screening conditions and the type of material, we can therefore improve the properties of polyurethane grilles.
In theory, abrasion loss in accordance with DIN 53516 can be used to compare the performance of various polyurethane grades. However, actual screening conditions on screening surfaces are far removed from this standardized test, and the choice of the best grade is usually based on the manufacturer's experience or on the in-house development of test procedures that are as close to reality as possible.
Independently of the choice of grade, the choice of hardness (expressed in shores) plays a major role in abrasion resistance. In fact, the nature, shape and mass of the materials screened produce impacts of varying degrees of sharpness, which in principle are better withstood by lower hardnesses. This is why two-layer constructions are commonly used.
In our case, the polyurethanes used are heat-castable and, given the requirements in terms of both mixing ratios of the various components and processing temperatures, the use of a casting machine is almost always indispensable.
The abrasion resistance of the screening surface depends directly on compliance with the processing conditions recommended by the material supplier (mold temperatures, firing temperature and time, steaming temperature and time). Here again, experience and care during the process will guarantee the product's final qualities.
That's why GIRON is constantly striving to design and manufacture ever more efficient equipment in terms of abrasion resistance. We regularly work with our suppliers to define the optimum formulation for our products. high-performance polyurethanes depending on the application, such as screening abrasive materials, underwater or dry screening, or many others.