Pentru a alege pânza de ecran potrivită, trebuie să înțelegeți cum se uzează. În timpul utilizării, abraziunea materialelor tinde să aplatizeze ecranele, erodând relieful. Rezistența la abraziune pentru a combate uzura materialelor de screening este, prin urmare, un obiectiv cheie în această alegere. Intră în joc mai multe variabile:
- Tipul de materiale utilizate pentru fabricarea sitelor de cernere: metal vs sintetic
- Aspectul suprafeței care intră în contact cu produsul care urmează să fie ecranat
- Calitatea sculelor și a procesului de fabricare a țesăturilor de screening
Alegerea oțelului
Un standard ISO definește condițiile prealabile pentru fabricarea pânzelor de ecranare (toleranțe, cerințe, metode de verificare etc.). Denumirea europeană de pânză din sârmă de oțel de înaltă rezistență poate duce la confuzie, deoarece este acceptată pentru sârmele cu o rezistență de peste 80 kg/mm². Numai această denumire nu este suficientă pentru a face comparabile pânzele de ecranare de la diferiți producători.
Majoritatea pânzelor de ecranare țesute în prezent sunt fabricate din aceeași calitate de sârmă de oțel, cunoscută sub denumirea de "sârmă de ecranare". Acesta este de fapt oțel carbon, foarte asemănător cu sârma de oțel pentru arcuri, a cărei rezistență finală este obținută în timpul procesului de tragere la rece.
Pentru fabricarea țesăturilor sale de screening, GIRON a selectat oțeluri cu caracteristici optimizate combinând un conținut de carbon de cel puțin 0,5% pentru a garanta o rezistență ridicată la uzură și o rezistență ridicată la absorbție fără fragilitate:
- Deformațiile necesare pentru preformarea firelor înainte de țesere
- Tensiuni mecanice cauzate de vibrațiile ecranului, chiar și la energii ridicate
- Șocuri de la materiale și produse care trec peste grile
Aspectul suprafeței rezultate în urma preformării
După cum am spus, uzura abrazivă apare atunci când materialele se freacă de suprafața de criblare. Prin urmare, este ușor de observat că, cu cât suprafața este mai plată, cu atât produsul care urmează să fie cernut va trebui să ronțăie mai puțin.
Prin urmare, tipul de preformare este foarte important pentru reducerea uzurii pânzelor de criblat, a căror durată de viață depinde de cantitatea de material care poate fi uzată fără ca ochiurile să se deformeze sau firele să se slăbească.
1. Preformă "val simplu" (model : Grilgirco)
Această preformă corespunde formelor A, B și C definite de ISO4783/3. Este cea mai elementară formă de ondulare a sârmei. Operațiunea constă în deformarea sârmei de oțel într-o formă sinusoidală simplă.
Țesutul acestor fire (urzeală și bătătură) produce o suprafață formată din denivelări și goluri, cu o diferență de nivel egală cu diametrul firului.
Din cauza unghiului de închidere relativ deschis la nivelul onduleurilor, acest tip de preformă este evident mai sensibil la impact cu cât raportul ochiuri/fire este mai mare.
În plus, sub efectul abraziunii, eroziunea sau uzura capetelor ondulate (protuberanțe) împiedică avansarea produselor și duce la ruperea firelor înainte ca suprafața de cernere să fie uzată cu adevărat.
Cu toate acestea, din motive legate de costurile de producție, această preformare este utilizată în mod obișnuit pentru cele mai mici deschideri ale ochiurilor și pentru cele mai fine tăieturi, în general mai mici de 10 mm.
2. Preformă "Half-notch wave" (model : Plangirco)
Această preformă corespunde formei D, astfel cum este definită de ISO4783/3. Această ondulație dreaptă este o evoluție a ondulației simple (forma A).
Căutarea unei mai bune rezistențe la abraziune a dus la dezvoltarea unei tehnici de preformare caracterizată printr-o amprentă mai pronunțată la punctele de intersecție ale fiecărui fir.
Țesutul acestor fire (urzeală și bătătură) are ca efect limitarea reliefului (protuberanțe) prin transferarea unei cantități cât mai mari de metal către suprafața de lucru, cu o diferență de nivel limitată la ½ din diametrul firului.
Prin urmare, durata de viață a țesăturii va fi îmbunătățită în comparație cu o simplă ondulare. Acest tip de preformare cu "jumătate de crestătură" este utilizat în mod obișnuit pentru ochiuri mai mari de 10 mm.
3 Preforma "suprafață plană ondulată" (model : Plangirco suprafață plană)
Această preformare corespunde formei E definită de standardul ISO4783/3. Această ondulație este ultima îmbunătățire a preformării sârmei în căutarea longevitate maximă a sitelor de cernere. Nu numai că practic nu există relief (denivelări) pe suprafața de cernere, dar cantitatea maximă de metal disponibil este transferată pe suprafața de lucru.
Prin combinarea ștanțării în unghi închis și a decupării firelor la fiecare punct de intersecție, această preformare elimină orice risc de deformare a suprafeței de ecranare până când grila este complet uzată.
Această preformare cu "suprafață plană" este în mod natural eficientă în domeniul său preferat de tăieri și ochiuri de dimensiuni medii (de la 10 la 40 mm), unde precizia tăierii cerută de standardele agregatelor și rezistența la abraziune sunt cruciale.
Durata de viață controlată pe numeroase instalații garantează o longevitate de neegalat, cu cel puțin 30% până la 50% mai mare decât orice alt tip de preformă.
GIRON utilizează această preformare "cu suprafață plană" ca standard de la ochiuri de 8 mm și pentru toate ochiurile care utilizează sârme cu diametre cuprinse între 4 mm și 8 mm.
Calitatea sculelor și a procesului de fabricare a țesăturilor de screening
Calitatea sârmei de oțel și tipul de preformare, deși foarte importante, sunt departe de a fi suficiente pentru a obține o plasă de cernere foarte bună. Dacă uneltele nu sunt bine concepute, dacă mașinile nu au puterea și precizia necesare, ochiurile nu vor fi regulate, iar sârmele se vor slăbi în timpul lucrului și se vor uza prematur din cauza lapajului.
Compania GIRON a dezvoltat și perfecționat propriile sale mașini, procese și tehnici unice pentru fabricarea de grilaje de oțel de foarte înaltă calitate.
Alegerea materialului
În prezent, nu există standarde specifice care să definească cerințele pentru fabricarea pânzelor de protecție sintetice (toleranțe, cerințe, metode de testare etc.). Două materiale de bază sunt utilizate în acest domeniu: cauciucul și poliuretanul.
Dar cum se definește un material de bază bun pentru fabricarea sitelor de cernere?
1. Cauciuc
Cauciucul este rezultatul transformării și amestecului omogen al mai multor ingrediente de origine și natură diferite. Inițial, cauciucul a fost obținut din latexul natural al anumitor plante (arbori de cauciuc). Odată cu dezvoltarea industrială și a noilor tehnici, cauciucul poate fi fabricat și pe cale sintetică (SBR, NBR etc.) din derivați ai combustibililor fosili.
Astăzi, procesele complexe de formulare și amestecare ne permit să obținem cauciucuri tehnice și de înaltă performanță pentru o gamă largă de aplicații.
Principalele proprietăți ale cauciucului sunt elasticitatea, impermeabilitatea și amortizarea. Acești trei parametri prezintă un interes deosebit în domeniul criblării, în special la prelucrarea granulometriei mari, pentru a absorbi șocurile sau a reduce zgomotul.
Cu toate acestea, necesitatea de a combate uzura rămâne primordială, iar alți parametri trebuie luați în considerare, cum ar fi rezistența la rupere, la căldură și la agenții chimici, utilizarea sa în timpul procesului de vulcanizare și condițiile de screening.
Prin urmare, cauciucul are proprietăți bune de rezistență la uzură cauzată de deformare și/sau tăiere. Cu toate acestea, grosimea trebuie să fie suficientă pentru a absorbi impactul materialului pe suprafața ecranului. În plus, unghiul de impact al materialului joacă, de asemenea, un rol esențial în nivelul de uzură, în special rezistența la rupere.
De asemenea, GIRON colaborează constant cu furnizorii săi pentru a defini formula optimă pentru produsele sale. cauciucuri de înaltă performanță în funcție de aplicație, cum ar fi filtrarea produselor fierbinți, a produselor chimice sau a produselor abrazive.
2. Poliuretan
Utilizați pentru prima dată în Germania în anii 1930, poliuretanii (o familie de polimeri) au devenit larg utilizați după cel de-al doilea război mondial, înlocuind nailonul și cauciucul.
Poliuretanul (funcția uretanică) este rezultatul reacției chimice a unui izocianat și a unui poliol.
Există trei familii tehnice principale: spume flexibile, spume rigide și non-spume.
Spumele reprezintă 2/3 din piață.
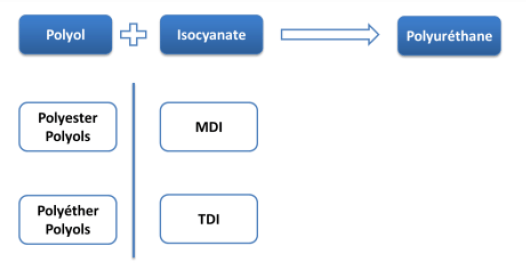
La sfârșitul anilor 1970, poliuretanul (o familie de substanțe care nu sunt spumă, inclusiv elastomeri, adezivi și acoperiri) și-a făcut apariția în screeningul materialelor și în tehnologia de prelucrare.
Ca și cauciucul, poliuretanul este rezultatul unor amestecuri și formule chimice complexe, în care alegerea ingredientelor permite atingerea unor niveluri diferite de performanță în funcție de aplicație. Totul este o chestiune de compromis.
Prin urmare, în funcție de condițiile de screening și de tipul de material, putem îmbunătăți proprietățile grile din poliuretan.
În teorie, pierderea prin abraziune în conformitate cu DIN 53516 poate fi utilizată pentru a compara performanța diferitelor tipuri de poliuretan. Cu toate acestea, condițiile reale de cernere pe suprafețele de cernere sunt departe de acest test standardizat, iar alegerea celei mai bune calități se bazează de obicei pe experiența producătorului sau pe dezvoltarea internă a unor proceduri de testare cât mai apropiate de realitate.
Independent de alegerea gradului, alegerea durității (exprimată în shores) este foarte importantă pentru rezistența la abraziune. Acest lucru se datorează faptului că natura, forma și masa materialelor ecranate produc impacturi cu grade diferite de asprime, care, în principiu, sunt mai bine suportate de durități mai scăzute. Acesta este motivul pentru care construcțiile cu două straturi sunt frecvent utilizate.
În cazul nostru, poliuretanii utilizați sunt turnabili la cald și, având în vedere cerințele în ceea ce privește atât raporturile de amestec ale diferitelor componente, cât și temperaturile de prelucrare, utilizarea unei mașini de turnare este aproape întotdeauna esențială.
Rezistența la abraziune a suprafeței de cernere depinde în mod direct de respectarea condițiilor de prelucrare recomandate de furnizorul materialului (temperaturi de turnare, temperatură și timp de ardere, temperatură și timp de aburire). Și în acest caz, experiența și grija în timpul procesului vor garanta calitatea finală a produsului.
Acesta este motivul pentru care GIRON face eforturi constante pentru a proiecta și fabrica echipamente care sunt din ce în ce mai eficiente în ceea ce privește rezistența la abraziune. Colaborăm în mod regulat cu furnizorii noștri pentru a defini formula optimă pentru produsele noastre. poliuretani de înaltă performanță în funcție de aplicație, cum ar fi cernerea materialelor abrazive, cernerea sub apă sau uscată și multe altele.